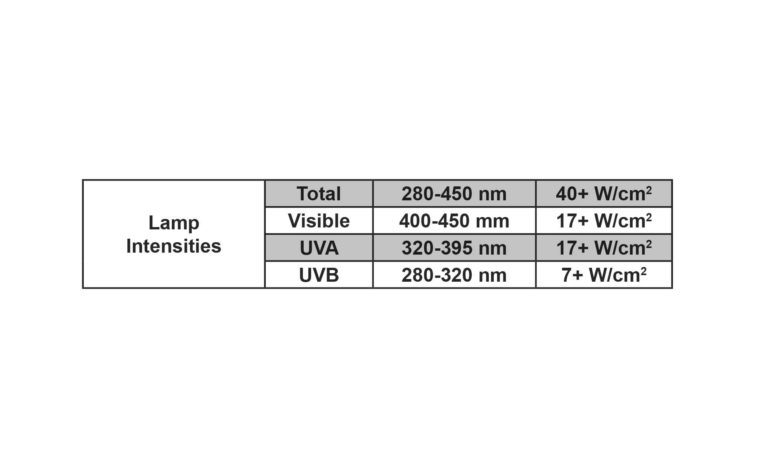
A Study on the Physical Properties of QSil 220 – A Silicone Potting Compound
Objective: To determine the physical properties of the potting and encapsulating silicone, QSil 220.
Instruments Used: M350-AX5 Tensile Meter, Jasco V-530 UV/Vis Spectrophotometer, Brookfield Viscometer DVII, Keithley Model 6517A Digital Electrometer/High resistance meter, Keithley Model 8009Resistivity Test Fixture, Reichert AR200 Digital Refractometer, Shore A2 Scale Durometer Gauge.
I. Tensile
First, the tensile strength of QSil 220 was studied in relation to the length of time the material was cured. The material was mixed with 10 parts A and 1 part B, de-aired, and then pressed at 150ºC for 15 minutes, 30 minutes, 1 hour, and 2 hours to make sheets. After the sheets cooled for 15 minutes the ASTM D412 was followed to determine the tensile. Results of all trials are listed in Table 1 and plotted in Chart 1. At 15 minutes, 1 hour, and two hours the average tensile was ~680 psi. The average of the material tested at 30 minutes was around ~500 psi, but this variation may be attributed to batch variation since this material was from a different batch. Overall, it appears that after 15 minutes the material is completely cured and can be heated for up to two hours longer without any variation in tensile.
II. Elongation and Young’s Modulus
The same method for making sheets was used to test elongation and young’s modulus. Dogbone samples were cut out using a Type “I” die cutter and then pulled on the tensile meter. The average elongation and young’s modulus was calculated to be 178% and 214, respectively. All other results are listed in Table 2.
III. Optical Transmission
The optical transmission of the QSil 220 material was evaluated in respect to wavelength, over the range 275nm to 1100nm, using a UV/Vis spectrophotometer. The acquired spectrum is listed as Plot 2.
IV. Viscosity
The viscosity of Part A and B were measured separately using a Brookfield Viscometer. Spindle #5 @ 20 RPM was used for both materials and the results were 4,400 cps for Part A and 5,000 cps for Part B. All viscosities were obtained when the temperature of the materials was between 20°C – 25°C.
V. Volume Resistivity
All measurements for volume resistivity were obtained following the ASTM D257. The measured volume resistivity of QSil 220, 3.80 x 1014 Ohm-cm, signifies that it the material is an insulator. All results are listed in Table 3.
VI. Dielectric Strength
The dielectric strength of the material was tested at an outside laboratory using a ¼ inch electrode. The average result was 511 V/mil with a standard deviation of 46 V/mil. Complete results are listed in Table 4.
VII. Durometer
The durometer of QSil 220 was measured at different length of cure using the ASTM D2240. About ~50 grams of catalyzed material was poured into four aluminum dishes and placed in the 150°C oven for 15 minutes, 30 minutes, 1 hour, and 2 hours. After the material was removed from the oven, it cooled at room temperature for 15 minutes and then the hardness was measured using a Shore A Durometer Gauge. All results are listed in Table 5 and plotted in Chart 3.
VIII. UV Testing
A cured sample of QSil 220 at ½ inch thickness was exposed to UV A, B, and C rays using a UV lamp. After 1,149 hours and 55 minutes, the sample was removed from the UV light with no visible signs of yellowing. The UV source was a Blue Wave 200 with the following lamp intensity:
IX. Work Life
Ten parts A and one part B were combined and left at 70°C for one week. At this point, the viscosity of the material was assessed and determined to be comparable to the initial catalyzed viscosity; thus, indicating that the work-life of the material is greater than 1 week or 168 hours.
X. Index of Refraction
Index of Refraction was measured at the sodium D-line, 589 nm, using a digital refractometer. At this wavelength, the RI of QSil 220 is 1.4080.
XI. Adhesion
The shear strength of the material was tested following the ASTM D1002. Two pieces of glass substrate were primed and then bonded together with QSil 220 so that the overlap was ~1/4 inch. Four samples were prepared and placed in the 150°C oven for 1 hr, 1.5 hrs, 2 hours, and 4 hours. After the samples cooled for 30 minutes they were clamped into the lap shears and pulled at a rate of 2.0 inches/minute. In every case, the substrate cracked before the adhesive failed resulting in no measurable values.
Conclusion
QSil 220 is available amongst a broad range of potting compounds and encapsulants developed by CHT. Finding the right silicone for your application is not limited to CHT’s product portfolio. Our technical team will partner with you to either modify specifications in a current product or custom formulate a new one to meet your exact requirements.
This is not the original. The canonical version can be found at https://www.quantumsilicones.com/informationcorner/silicone-potting-compound-a-study-on-the-physical-properties-of-qsil-220/