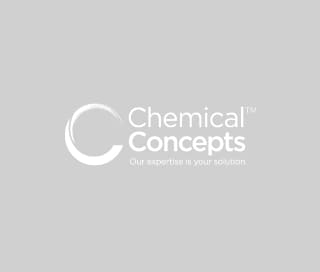
Types of MMD Equipment (Part 2)
So far, we have defined 2 of the 5 types of MMD equipment and explained their specific advantages in the workplace. Today, we’re going to finish off this two-part series and define the final three types:
- Proportioner Systems (Double Acting Piston Pumps)
- Gear Meters
- Gerotors
These three types of MMD equipment are very different and have specific functions in which they excel. Today, we will highlight the key differences between each system and help you determine which system is best for every project.
Proportioner Systems (Double Acting Piston Pumps)
Proportioner systems operate similarly to rod or piston meters, the exception being that proportioner systems can distribute two-component adhesives more smoothly than rod or piston meters. Because of the double-acting pistons, adhesive is dispensed from both pistons on each stroke.
The nature of proportioner systems also eliminates the refill stroke of a normal piston. As the piston or rod moves to the left, adhesive fills the right side and dispenses from the left side of each pressure cylinder.
Much like rod or piston meters, the identical pistons or rods displace equivalent volume from each pressure cylinder with each stroke. Decreasing the diameter of one piston or rod changes the mix ratios from 1:1 to 2:1, 4:1, etc.
Note: Pistons are also called plungers which are cylindrical that go in and out of correspondingly shaped chamber in a pump head. Inlet and outlet lines are joined to the piston chamber includes two check valves or ball valves. Metering rate can be adjusted by varying stroke length.
Gear Meters
Gear meters work by dispensing adhesive via interlocking gears driven by a common drive motor. The volume of the cavity created by the gear teeth determines the volume output of the equipment. For example, smaller gears create a wider space between teeth, therefore allowing for a higher volume output of adhesive.
As is true with all metering pumps, gear meter mix ratios are controlled by pairing two pumps with the same volume, running at the same rpm. Pairing a smaller volume pump or reducing the rpm of the second pump changes the mix ratio from 1:1 to 2:1, 4:1, etc.
A benefit of the gear meter system is a strong, continuous flow of adhesive; this system is ideal for high-volume applications and does not get clogged with high-viscosity adhesives.
Note: By using a closed-loop feed back control flow rate can be maintained by adjusting motor speed as the pressure varies. Gear pumps are also Hydraulic. Hydraulic is powered by fluids.
Gerotors
Gerotors operate by dispensing fluid through the cavity formed from the rotation of an asymmetric impeller. Impellers create a vacuum-like space between the vanes, which moves the adhesive through the cavity smoothly for continuous, high-volume applications. When moved by fluid, this is referred to as hydraulic.
Each gerotor operates using a common drive motor, so the speeds can be adjusted to rotate in unison for a 1:1 mix ratio or the rpm can be adjusted for a 2:1 or 4:1 mix ratio.
It is important to note that gerotors are NOT compatible with glass bead-containing adhesives; the glass beads can easily clog the impeller system and cause equipment failure. Gerotor pumps are, however, the most cost-effective method of metering materials at very high throughputs.
MMD equipment can be hugely beneficial in a large-scale project requiring high volumes of adhesive. With the knowledge of which system is best for your project, you can get the job done in no time! Unsure of which system is right for you? Our representatives are here to help. Please do not hesitate to reach out! Call us, toll-free, at 1-800-220-1966 or send us an email at sales@chemical-concepts.com. We look forward to speaking with you!